Microstructure Control in Materials
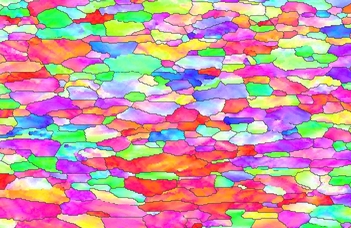
Microstructure Control in Materials Research Group
The core activities are related to the development of polycrystalline systems with predefined properties via tunning thermomechanical processing parameters. The research focuses on the design of advanced materials, experimental characterization of microstructures and modelling of technological processes. In the field of innovative manufacturing, the impact of technological parameters on product properties is less known compared to conventional processes and initial results indicate promising research directions. The main objective is related to the integration of multiple efficient modelling strategies and creation of a virtual manufacturing platform that not only enables the production of materials in a virtual space but also ensures control over real manufacturing processes and allows for in-situ changes in manufacturing parameters depending on the desired final properties. Thus, multiple hidden aspects of manufacturing processes can become apparent.
Thermomechanical processing of polycrystalline materials
Deformation: Symmetric and asymmetric rolling, tension, bending
Heat treatment: Conventional (~50°C/min) and ultrafast (~1000 °C/min) heating processes
Investigation of mesoscopic changes in materials: microstructural and crystallographic aspects
Structural and substructural evolution during deformation and heat treatment processes.
Details:
https://doi.org/10.1016/j.msea.2010.09.023
https://doi.org/10.1016/j.scriptamat.2012.10.039
https://link.springer.com/article/10.1007/s10853-014-8068-8
https://doi.org/10.1016/j.msea.2023.144768
https://doi.org/10.1016/j.msea.2022.143145
https://doi.org/10.1016/j.actamat.2020.03.049
https://doi.org/10.3390/ma17246057
Virtual Thermomechanical Processing of Materials
Generation of virtual structures based on experimental evidence.
Modelling the deformation processes by the finite element model, flow-line method and a vast variety of analytical approaches.
Process parameter influence on properties of materials.
Details:
https://link.springer.com/article/10.1007/s11661-013-2021-3
https://doi.org/10.3390/met9101098
https://link.springer.com/article/10.1007/s12289-016-1330-7
https://doi.org/10.3390/app13074359
https://iopscience.iop.org/article/10.1088/1757-899X/1121/1/012046
https://doi.org/10.3390/met15010011
Modelling the evolution of crystallographic texture and texture-based properties in materials by principles of continuum mechanics and crystal plasticity theory
Modelling the texture evolution during deformation employing Taylor-type crystal plasticity homogenization schemes: Full Constraints Taylor model, Visco-Plastic Self-Consistent model, Advanced Lamel model, Cluster V model.
Modelling the crystallographic features of microstructure evolution during heat treatment processes.
Modelling the plastic anisotropy in metals by various crystal plasticity approaches.
Details:
https://doi.org/10.1016/j.actamat.2008.01.042
https://doi.org/10.1016/j.msea.2008.03.005
https://doi.org/10.1016/j.ijplas.2014.08.009
https://doi.org/10.1016/j.actamat.2015.05.035
https://doi.org/10.1080/02670836.2016.1180742
Assessment of substructure evolution by indentation techniques and numerical approaches
Investigation of the evolution of geometrically necessary dislocations by orientation imaging microscopy.
Study of substructure development by micro and nanoindentation techniques.
Modelling the evolution of dislocation density in metals after various deformation degrees by a variety of numerical approaches.
Details:
https://doi.org/10.3390/met11101571
https://doi.org/10.1016/j.matchar.2022.112166
https://doi.org/10.1016/j.msea.2023.144768
https://doi.org/10.1016/j.matchar.2025.114764
Study of softening kinetics and annealing phenomena in materials
Experimental study of softening phenomena in materials by means of orientation imaging microscopy and indentation techniques .
Modelling the kinetics of recrystallization in polycrystalline aggregates.
Details:
https://mmelo.eu/event/online-lecture-by-prof-jurij-sidor/
https://doi.org/10.1016/j.actamat.2011.05.050
https://doi.org/10.3390/ma16175760
https://iopscience.iop.org/article/10.1088/1742-6596/2635/1/012031
https://www.scientific.net/SSP.353.53
https://iopscience.iop.org/article/10.1088/1757-899X/375/1/012028
Materials Characterization by Scanning Electron Microscopy, Electron Backscattering Diffraction and Electron Dispersive Analysis
The scanning electron microscope FEI-Teneo, equipped with FEG source, ensures high resolution images. The microscope is also equipped with the EBSD and EDX detectors enabling both measurements of crystallographic texture in materials and chemical analysis
Testing of Mechanical Properties on Macroscopic, Microscopic and Nanoscales
Macroscopic Properties by Tensile/Bending and Charpy testing: yield stress, ultimate strength, ductility, hardening parameters, Young modulus, Poisson ratio, toughness, Lankford value, impact energy.
Microscopic properties: Vickers and Knoop microhardness measured with the loads ranging between 10gf to 1 kgf.
Local indentation measurements by nanoindenter with Berkovich tip (loads ~ micronewton).
Numerical Approaches used for through process modelling: Finite Element Models, Flow Line Models, Crystal Plasticity Models, Recrystallization Models
Both well-established continuum-mechanics based approaches such as Finite Element Models as well as computationally efficient numerical methods such as Flow Line Models are used for the simulation of virtual processing of materials.
The crystallographic aspects of microstructure evolution and hardening are simulated with various crystal plasticity codes.
The kinetics of recrystallization and other annealing phenomena are simulated by the numerical approaches developed in our group.
- Prof. Dr. Jurij Sidor, DSc, Group Leader
- Dr. Fenyvesi Dániel, Associate Professor, Senior Researcher
- Dr. Borbély Tibor, Associate Professor, Senior Researcher
- Dr. Herbáth Beáta, Senior Researcher
- Bátorfi János, PhD Student, research assistant
- Tóth János, research technican
- Number of BSc and MSc Students are employed for conducting project subtasks.
Grants and/or Government supported research projects
- Security and data protection in the fields of material technology, industry 4.0 and energy engineering (2022-2025, pillar 3 in the project no. TKP2021-NVA-29 “Protection of high integrity national services and industrial infrastructures using cybersecurity, technological and legislative instruments”)
- Innovative processing technologies, applications in energy engineering, and wide-range microstructure investigation techniques (2017-2021, workgroup 5 in the project EFOP-3.6.1-16-2016-00018 “Improving the role of research + development + innovation in the higher education through institutional developments assisting intelligent specialization in Sopron and Szombathely”)
- OTKA. Modelling and complex experimental evaluation of texture dependent solid phase reactions in metallic systems (Project nr.: 119566)
- OTKA. New avenues of production of bulk and composite nanostructured metals; experiments,characterization, modelling. (Project nr.: 143800)
Industrial Projects
- 2016: Microstructural investigation of MnZn ferrite. Industrial Partner: EPCOS Kft., TDK Group Company.
- 2019: Scanning electron microscopy: material examination by SE/BSE and EDX detectors. Industrial partner: Schaeffler Savaria Kft.
- 2020: Determination of mechanical properties by tensile, bending and Charpy methods. Industrial partner: Alpok Projekt Kft.
- 2021: Determination of microstructural differences by microhardness, scanning and optical microscopy. Industrial partner: BPW-Hungária Kft.
- 2021: Assessment of properties by microhardness and SEM. Industrial partner: iSi Automotive Hungary Kft.
- 2022: Determining the thickness of different layers using an optical microscope. Industrial partner: BPW-Hungária Kft.
- 2022: Fracture surface studies: Optical and Scanning Electron Microscopy. Industrial partner: Schaeffler Savaria Kft.
- 2022-2024: Development of Parabolic Spring. Industrial partner: BPW-Hungária Kft.
- Sidor, J., Miroux, A., Petrov, R. and Kestens, L. (2008) ‘Microstructural and crystallographic aspects of conventional and asymmetric rolling processes‘, Acta Materialia, 56, pp. 2495–2507.
- Sidor, J., Petrov, R. H. and Kestens, L. A. I. (2010) ‘Deformation, recrystallization and plastic anisotropy of asymmetrically rolled aluminum sheets‘, Materials Science And Engineering A, 528, pp. 413–424.
- Sidor, J. J., Verbeken, K., Gomes, E., Schneider, J., Calvillo, P. R. and Kestens, L. A. I. (2012) ‘Through process texture evolution and magnetic properties of high Si non-oriented electrical steels‘, Materials Characterization, 71, pp. 49–57.
- Sidor, J. J., Decroos, K., Petrov, R. H. and Kestens, L. A. I. (2015) ‘Evolution of recrystallization textures in particle containing Al alloys after various rolling reductions: experimental study and modeling‘, International Journal of Plasticity, 66, pp. 119–137.
- Chakravarty, P., Pál, Gy., Sidor, J. J. (2022) ‘The dependency of work hardening on dislocation statistics in cold rolled 1050 aluminum alloy‘. Materials Characterization, 191, pp. 112166:1–112166:13.
http://smi.inf.elte.hu/laboratechnika/
Savaria Institute of Technology
Present collaborations
Former collaborations